5-30t/h Dry Mortar Production Line
Message
A plant for the production of dry building mixtures (CCM) can differ significantly from one another in terms of capacity, technical skills, equipment composition and degree of automation. Plants are designed according to the specific technical requirements of each customer.
The plant includes:
- Equipment for sand preparation (drying and classification);
- Equipment for dosing components of the mixture
- Equipment for mixing and packing;
- Control system.
- Equipment for feeding the mixture components;
- Optional equipment
Sand preparation equipment
To obtain high quality mixtures, all the initial components of the mixture must be dry. The moisture content of the sand should be not higher than 0.5%. For sand drying, three-circuit drum dryer or single tank rotary dryer are used. After drying, Feeding dry sand on vibrating screens with 1, 2 or 3 sieve frames (usually with a mesh size of 0.63, 1.2 and 2.0mm respectively) for classification . After classification, sand will be conveyed in bunkers for cooling to the required temperature, then each size will be fed to the dosing unit and mixer.
Mixture metering equipment
In order to improve the production efficiency of the equipment, improve the accuracy of the batching part and reduce maintenance personnel, the mixing and feeding are also equipped with an automatic batching system. Therefore, the mixture according to the predetermined program will be automatically added to the metering hopper in sequence. In order to ensure the highest productivity, the mixing machine has the least loss of loading and unloading time (each cycle does not exceed 1 minute), and all three main technical operations (metering, mixing and filling the final mixture) are performed simultaneously.
Mixing and filling equipment
Control system
low class
medium level
Top level
Equipment for feeding mixture components
Optional equipment
For normal operation of the plant for the production of dry mixes, it is necessary:
1. Dust collector ---- Install a centralized aspiration system, connect it to dispensers and dispensers.
2. Compressor --- Provide a supply of compressed air with a pressure of at least 0.6 MPa with a flow rate of 600 l / min.
At the work site, the customer himself prepares:
1. To supply sand to the feeder hopper, use a front loader with a bucket lifting height of at least 2.5 m and a bucket volume of 0.4 ... 0.8 m3.
2. Use an electric forklift to move pallets with products and FIBCs.
3. Power supply
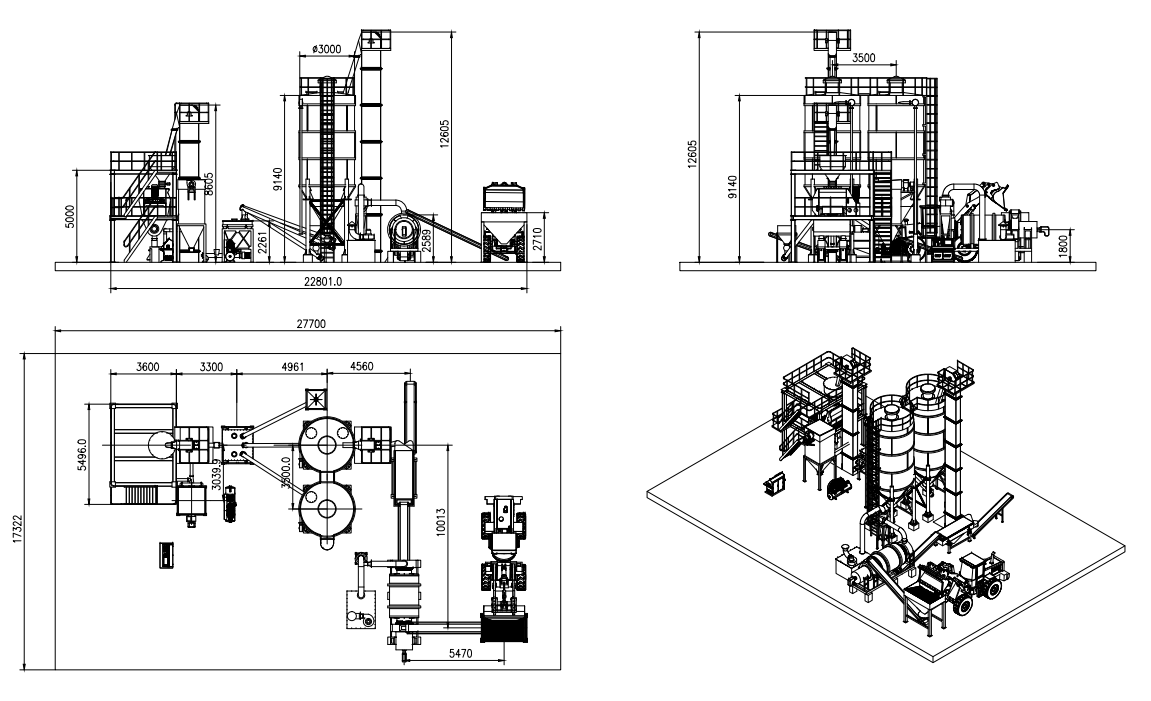
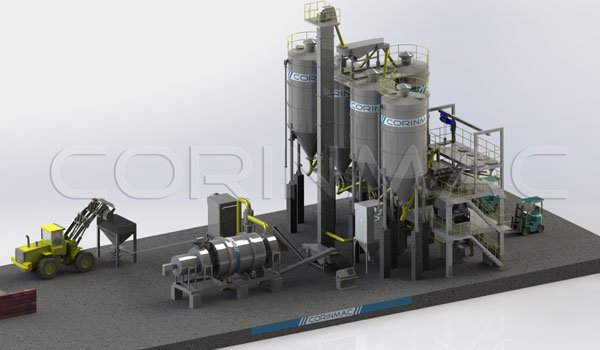
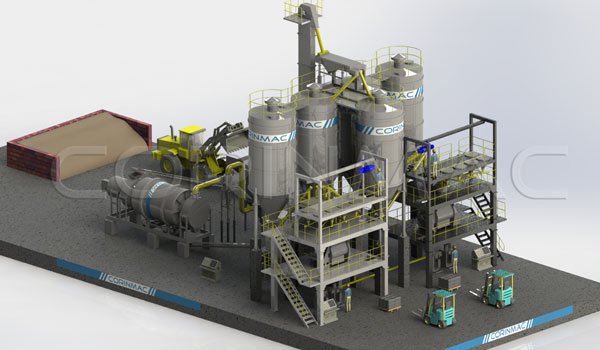
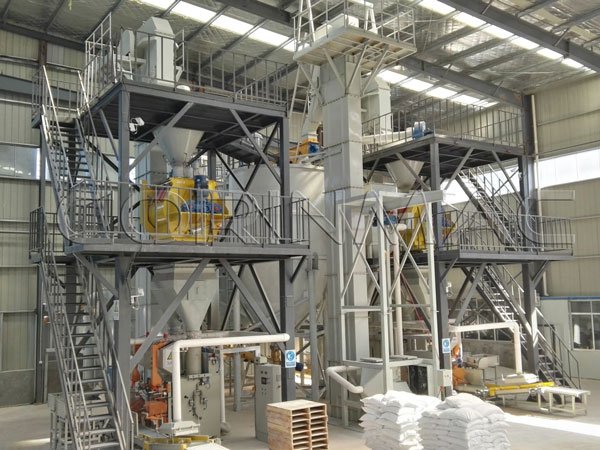
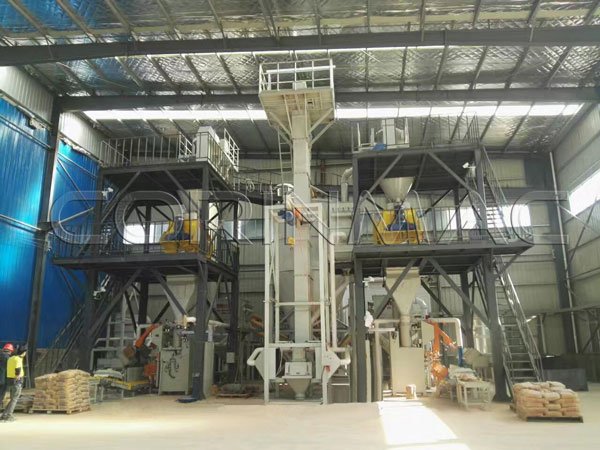

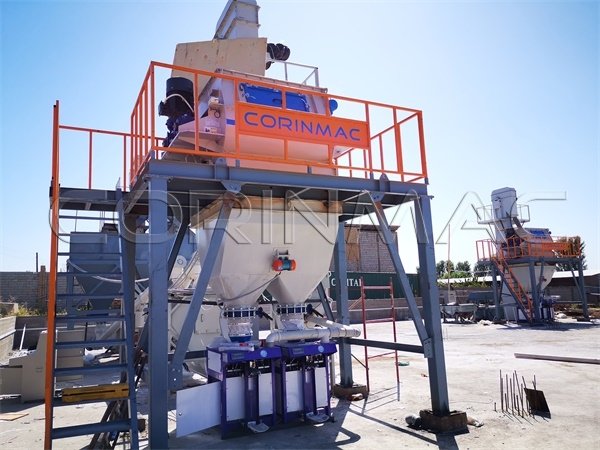
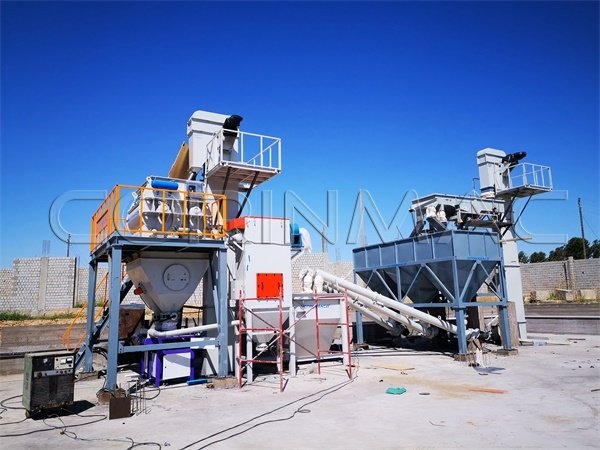
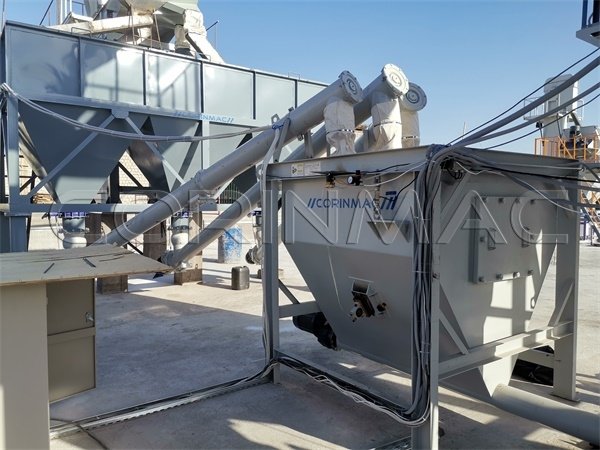
Specifications
Capacity(t/h) | 5-10 |
Formula setting(group) | Multiple formula can be set according to different proportions |
Adhesive | Portland cement, slaked lime, gypsum, soda slag |
Aggregate | Quartz sand, fly ash, slag, white ash, talc, etc. |
Raw material measuring switch | Dosing (Auto / Manual) |
Additive measuring switch | Dosing (Auto / Manual) |
Package weight (kg) | 10-50 |
Installed power (kw) | 20-200 |
Power supply voltage (V) | 380 |
Current frequency (Hz) | 50 |
Minimum material temperature ° C | 10 |
Maximum material temperature ° C | 80 |
Raw material humidity% | 0,1 |
Raw material bin volume | Make different volumes according to customer needs |